top of page
The Tower at PNC Plaza
Pittsburgh, Pennsylvania
Olivia Eckard
Lighting | Electrical
Building Statistics Part II
General Building Data
Building Name | The Tower at PNC Plaza
Location & Site | 314 Fifth Avenue | Pittsburgh Pennsylvania
Building Occupent Name | The Tower at PNC Plaza
Occupancy or Fuction Types | Office Complex [B]
Size | 800,000 SF
Number of Stories | 33 stories above grade | 37 total levels
Dates of Construction | Spring 2012 - October 2015
Overal Project Cost | $240 million
Project Delievery Method | CM at Risk

Project Team
Owner | The PNC Financial Service Group, Inc.
Architect | Gensler
Sustainablity Consultant | Paladino & Company
MEP & Structural Engineer | Buro Happold
Landscape Architect | LaQuatra Bonci Associates
Civil Engineer | Civil & Environmental Consultants
Lighting Designer | the studioi company
General Contractor | PJ Dick
Acoustical Consultant | Pin Drop Acoustics
Facade Consultant | Heintges
Lighting
LEDs are the main sources for the lighting system, along with a fluorescent source used in one space. Specialty lighting is used in the auditorium for the stage area and large decorative pieces are used throughout spaces such as, the lobby, neighborhoods, and dining area. Daylight is largely used effectively to light many spaces, especially the lobby and neighborhoods. Occupancy and daylight sensors are used throughout the Tower for control of the systems, with also additional specialty control in the auditorium and a control schedule for the lobby lighting.
The building will run on 480/277 3PH to fuel the buildings electrical systems. 208/120V is used at certain locations of the building to transform the voltage by the use of 75kVA step-down transformers for power receptacles and certain mechanical equipment. The electrical system is backed up by an emergency 2500kW 480/277 3PH diesel generator for life safety and fire control. A UPS backed dry type transformer is used for the typical office floors and is used for the chiller will prevent a reboot of both circuits upon a failure of the normal power service.
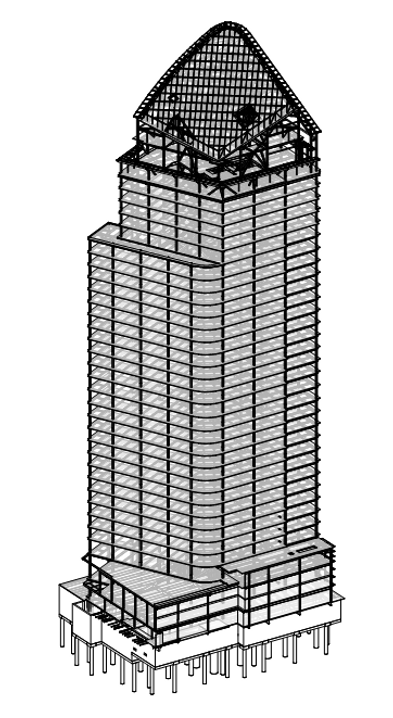
Electrical
Structural
The Tower is composed of a seismic force resisting steel braced frame. 50 and 65 ksi size W-shapes were used for all trusses, core columns, core braces, and core beams. There is also an underground parking garage, which requires a deep foundation where caissons are used that range from27’ – 6 ¼” to 33’ – 0” deep.
Construction
CM at-risk was the project delivery method that was used, and construction was performed by PJ Dick. The tower was constructed from Spring 2012 to October 2015. Upon completion, the building came to $240 million and plans to exceed LEED Platinum. To define what is beyond LEED Platinum, the project team created goals that would be implemented into the Tower, along with technologies that would optimize these goals.
Telecommunications
CM There are two telecom service entrances on basement level 1, one on north side and one on the south. On level 3, the conduit runs to the carrier units room where where the main distribution frame is located. Then on each level, individual intermediate distribution frames are located that interconnect and manage the telecommunications wiring between the MDF and the workstations.

Mechanical
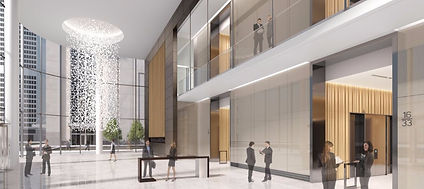
The double skin façade of the Tower consists of mechanically operated poppers that allow for natural ventilation, that will pop with the building is at optimal weather conditions. A solar chimney is what pulls the air in through these open windows, rather than sucking air out. Shaping the top of the tower to over a 25 degree angle optimized for solar collection. By doing this last step, it created a cooling effect by drawing warm air out of the tower. Then air fills the cavity through the automated slots and open dampers in the inner skin, allowing for the office to be in 100% passive mode with fresh air.
Level 33 contains the mechanical penthouse that houses air handling units and a cooling tower with a nominal capacity of 1300 tons. There is a total of 9 air handling units that are throughout the Tower. On the mechanical penthouse level, an air handling unit serves the upper atrium, providing a total of 15K CFM. Also on the penthouse are 3 more AHUs that serve office blocks, providing 90K CFM total (30K CFM each). Level 3 has two more AHUs that serve the auditorium prefunction space (10K CFM) and the cafeteria (9K CFM). On the 2nd level, 3 more AHUs provide air to the auditorium (11K CFM), lobby (10K CFM), and the business center areas, such as meeting rooms with 2,500 CFM. A chilled beam system is used throughout the building.
Fire Protection
Transportation
The Tower has two fire pumps, one 125 HP and 100 HP. Both are connected to the main collector BUS and directly connected to the emergency generator. Throughout the building are automatic sprinklers and fire command video wall monitors. The building has a digital, addressable fire-alarm system which will send a signal to initiate smoke detectors, preaction system, fire standpipe system, and a few other signals.
A total of 16 elevators serve the Tower. 12 of these are accessed on the lobby of the first floor, while half are meant for the entire building, called “high-rise elevators” and the other 6 are called “low-rise elevators.” 2 others are parking elevators for the underground parking below. Also, there are 2 service elevators for access during a fire.
Security
Security and safety systems consists of a video surveillance system, access control, intrusion detection/environmental sensors, intercom communications and surge and lightning protection. At the lobby entrance there is security with a card reader, to allow access to the elevators.
bottom of page